Classic Mini Cooper rockers, push rods and more!
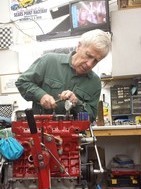
Shop Pushrods
When you are trying to build a motor to get the ultimate of performance you often will also optimize the life expectancy of the entire assembly. One such area centers around the rocker assembly. In general the rockers are part of the process that translates the lobe of the rotating camshaft to the vertical deflection needed to open the valves on the cylinder head. On a stock Mini the rocker is also designed to slightly amplify the movement with a rocker that is slightly longer on the valve side of the rocker than on the pushrod side; ie. For every .1” the pushrod is moved, the valve is deflected .125”. As the pushrod rides up on the cam lobe the vertical movement is translated to the rocker that pushes down on the valve.
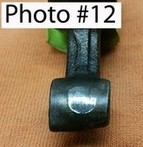
Rocker geometry in our vintage motors is a series of compromises and a lot has been written on the numerous, very complex factors that are in play with rockers. They indeed can have a very dramatic impact on performance. We often spend a lot of time & money picking a camshaft that has been designed and ground within extremely tight tolerances. We then set the camshaft timing to within a degree or so of the optimum. And then we throw on a set of rockers and say all is good?? Rocker geometry can not only change valve lift but even camshaft timing itself. To make matters worse it could be different from one rocker to the next!
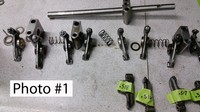
The first step is to measure each of the rockers (Photo #1) in a manner that only tests the rocker and avoids all the other variables such as the height of each valve, wear on the tip of the valve, and depth of the valve in the valve seat. The easiest way to do it is to strip a rocker assembly down to two pedestals only and put them back on the head with one pushrod in number one position. With the adjustment backed all the way off you can typically slide each rocker on and off without having to remove the shaft. As shown in photo #2 you then simply place the dial indicator on the spring retainer and rotate the engine thru a cycle to find total valve lift.
The
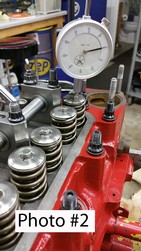
The next step in the process is to establish the center line of the rocker pivot point in relationship to the pushrod on one end and the valve tip on the other. While often debated we have concluded that the optimal vertical location is such that the valve tip, the pivot point at the pushrod, and the center of the rocker be as close to horizontal as possible when the valve has
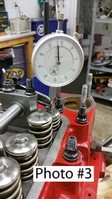
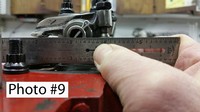
The final step in the process is multifaceted. As the ends of the rockers move in an arc, they also go up & down. The pushrod holes in the head are extremely small (and poorly aligned) and it is critical that you closely watch that the pushrod does not hit on the side of the head as it goes up and down. (Photo #5) The location of the rocker on the shaft horizontally is easy enough to set with shims. The real challenge is to have close-to-center contact of the
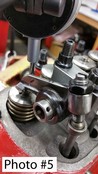
A few final cautions to be observed during final assembly; be sure the front of the rocker pedestal spacers are not interfering with the bottom edge of the springs. Be sure to cycle the engine a number of times before finally torqueing the head bolts to be sure that everything is seated in place. Be sure to set the valve rocker clearance per the camshaft manufacturer specs before starting the motor.